Naoko Nakui researches Shinafu, an ancient Yamagata fabric, and a world-class, ultra-fine mohair yarn.
She first visits the Sekigawa district of Tsuruoka City to discover an ancient weaving technique using threads taken from the bark of two Japanese lime trees, the shinanoki and obabodaiju. Before the dissemination of cotton, in regions little blessed with fabric-making materials, the people used these tough, water-resistant threads for everything from work clothes for use in the wet fields to fishing nets and sake strainers.
A handspun knitwear maker in Sagae City now uses traditional machinery to make truly unique yarns that cannot be found anywhere else. Its output includes world-class, ultra-fine mohair threads.
These Snow Country yarns link the past, present and future and provide insights into the fundamental nature of thread-making.
Naoko Nakui Book Designer
Ancient and World-class Thread
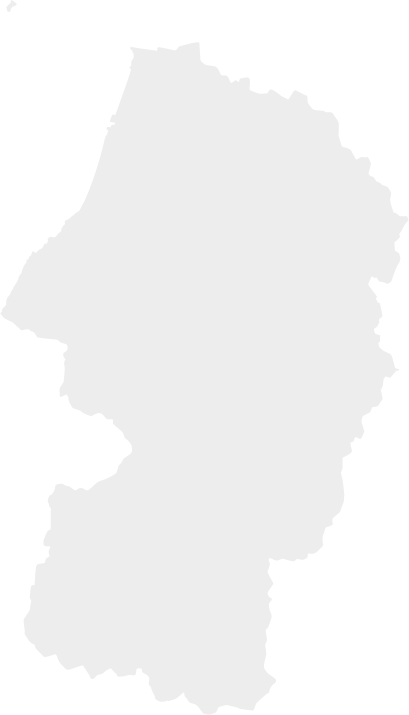
DESIGN TREASURE
Thread-making Design in the Snow Country
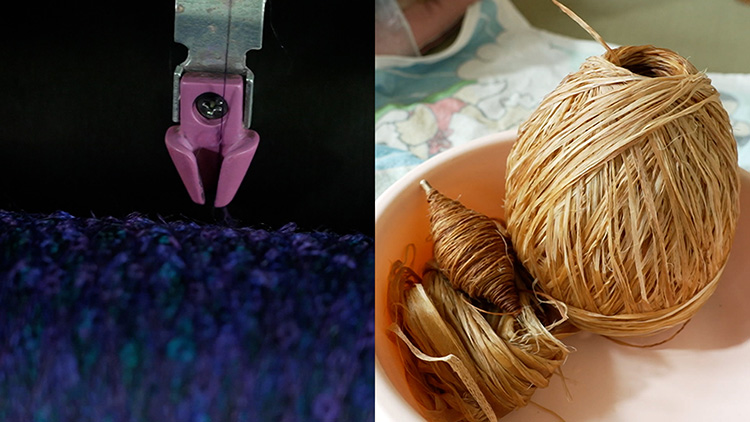
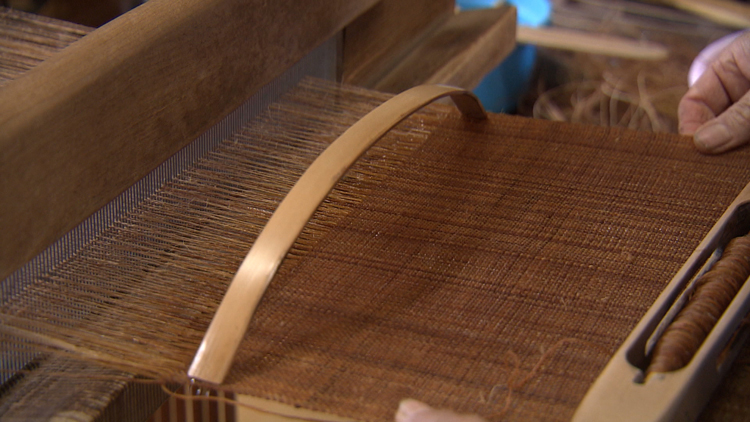
UETSU Shinafu (Bark Fiber Textiles)
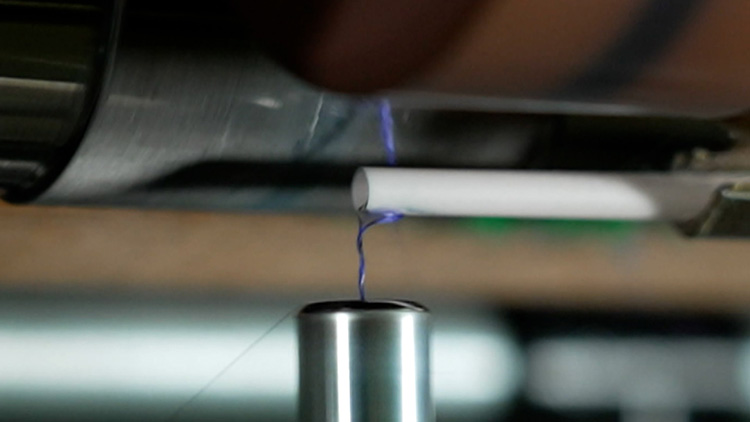
Spinning of ultrafine mohair yarn
CREATOR
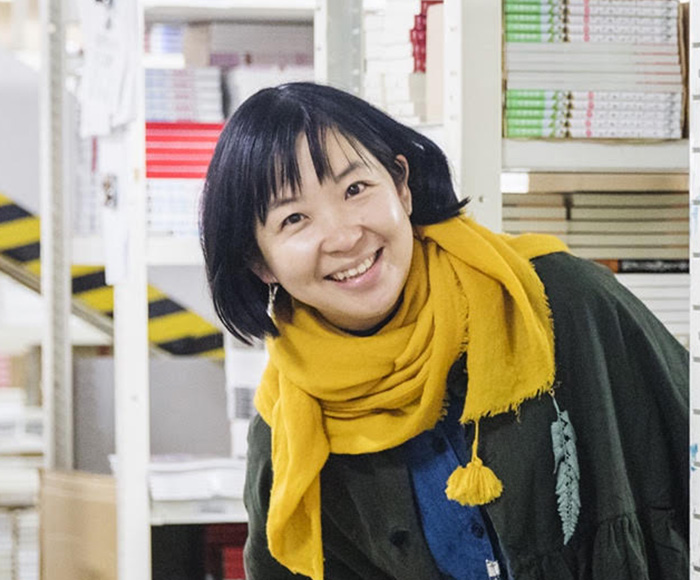
Photo by Sayuki Inoue
Naoko Nakui Book Designer
Born in Iwate in 1976.
Nakui went freelance in 2005 after starting out at an advertising agency. She designs from novels to picture books and dictionaries, and won various book design awards, including for Mieko Kawakami’s Ai to Yume toka. She has also designed the bindings of works by such authors as Kotaro Isaka, Yoko Ogawa and Tomoka Shibasaki. Bronze Medal in BEST BOOK DESIGN FROM ALL OVER THE WORLD in 2022.
A tradition constantly maintained as a part of daily living
The Sekiguchi district where Shinafu fabrics are made is located in the borderlands of Yamagata and Niigata Prefectures. This is the Snow Country, where snow piles up to a depth of two meters in winter.
Much of the yarn-making work requires physical strength. Nakui observes, “The tradition would be hard to conserve without the cooperation of the entire community.” More than 20 processes are involved in the year-long task of making the yarn from the bark and producing the fabric. Nakui respects how the time-consuming and painstaking nature of the work is taken for granted, and the practices continue even now as an integral part of the people’s daily lives.
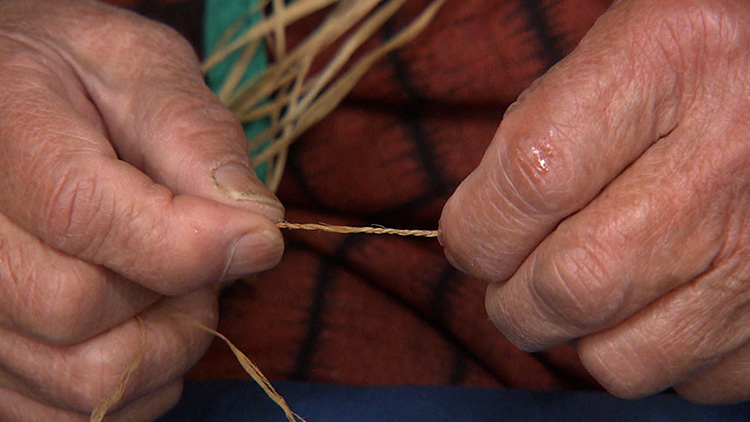
Bark torn and twisted into long threads
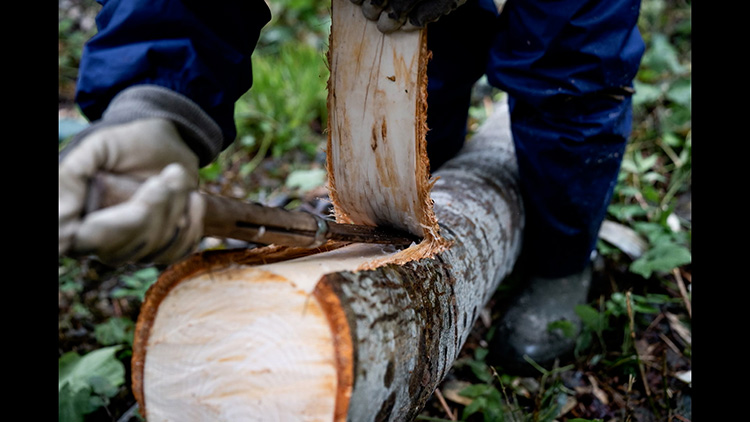

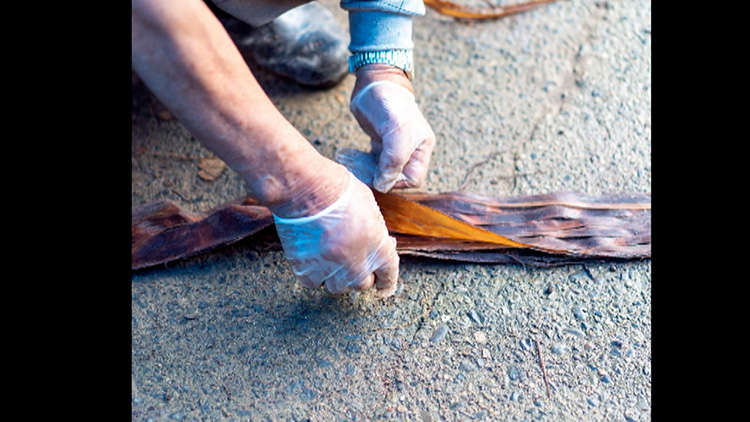
Peeling the bark (left), Soaking (center), Peeling off the bark layer by layer (right)
Photo by Joe Igarashi
The interaction with old machines opens up new vistas
Nakui is surprised by “the creative work that weaves products the whole world will admire.” This factory uses machinery that is more than 60 years old. Its very oldness makes improvements possible to produce things that nobody anywhere else can make. This is aggressive yarn-making, and the factory even stretches a single gram of mohair to a length of nearly 50 meters, making thread half as thin again as the previously supposed limit. “The output from the machines changes depending on the skill of the minder,” says Nakui. The machine and craftworker become one in this process of using the old to create the new. Nakui is entranced by a design process born from the urge to keep on making small, incremental improvements.
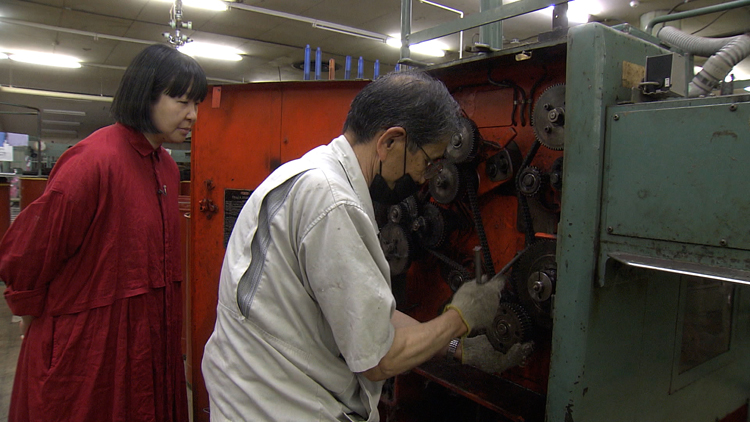
Craftsman adjusts a machine

Comparison of pre-twisted and twisted wool fiber
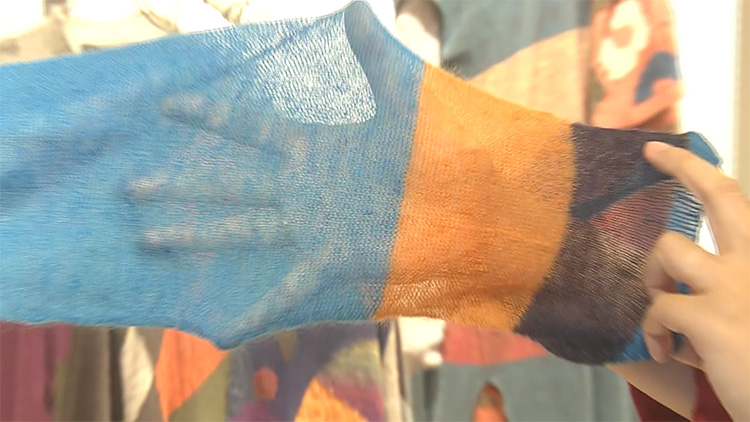
Transparently thin, lightweight, and warm ultrafine mohair yarn knit
Yarn is fundamental. It is the strongest. It does not grow old. I feel the power of its inclusiveness.
“My understanding of yarn was too narrow,” says Nakui. The paper, too, that Nakui handles in her regular work differs depending on whether it is flat or threaded. At root, this is also about the thread. She realizes, “If the yarn permits fine work, it doesn’t matter really whether it is made from bark or wool. The fundamentals of yarn can be free.” Also, she feels that the longer the harsh winters continue, the more the intense dedication to yarn-making in Yamagata “has both passed methods down firmly across the years and become a part of the people at each moment in time.”
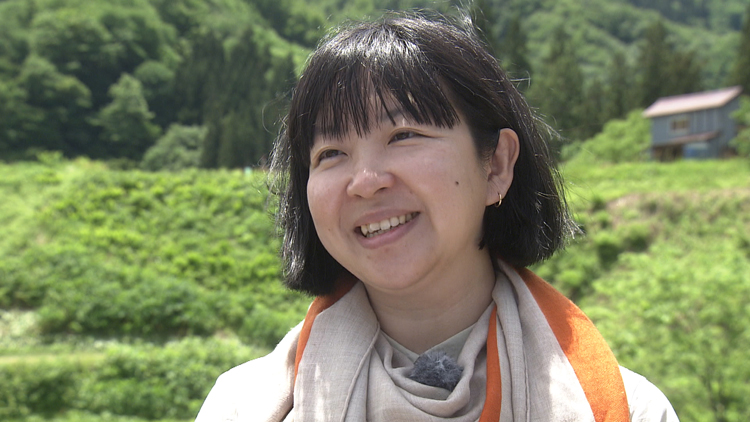
Nakui looking back on her research
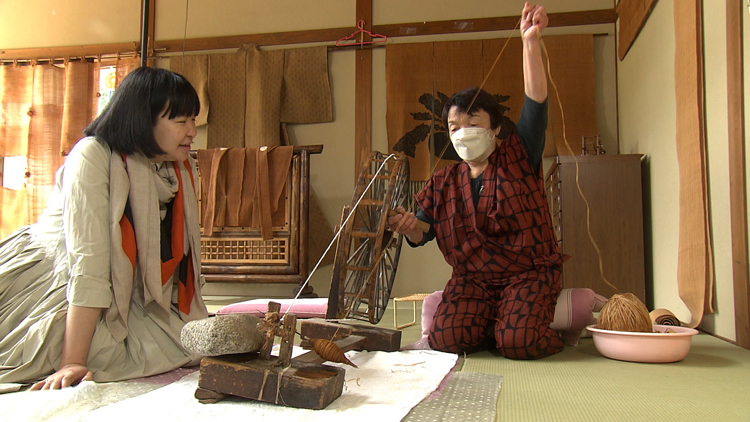
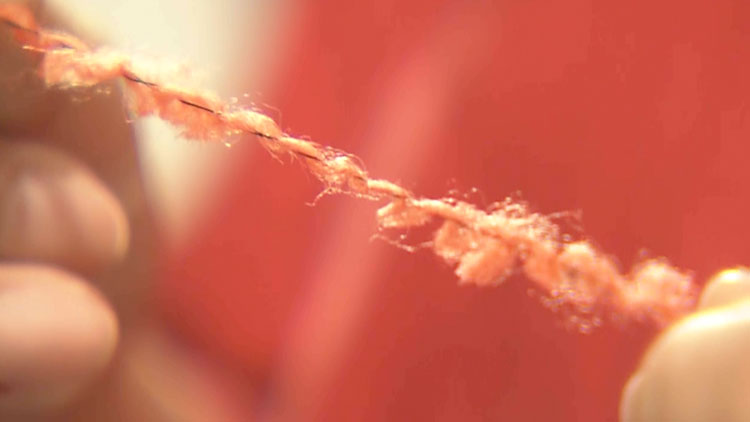
Where Can We See This Design Treasure?
Shinaori Center
222 Sekigawa, Tsuruoka, Yamagata 999-7315
Click here for more details.
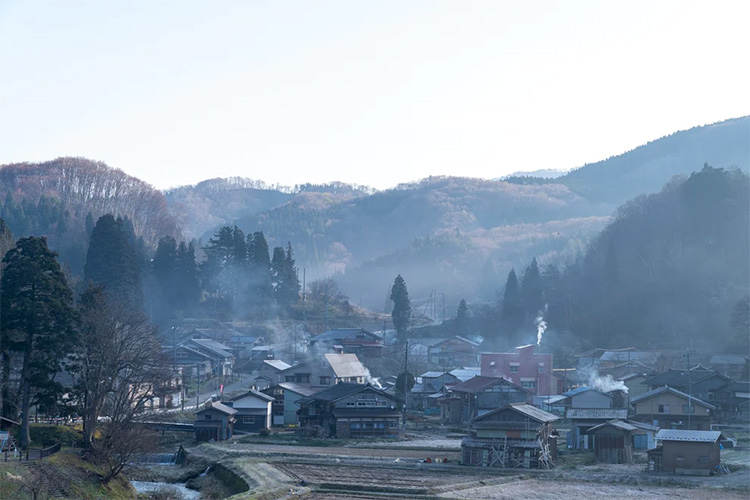
GEA
1-19-1 Motomachi, Sagae City, Yamagata 991-0053
Click here for more details.
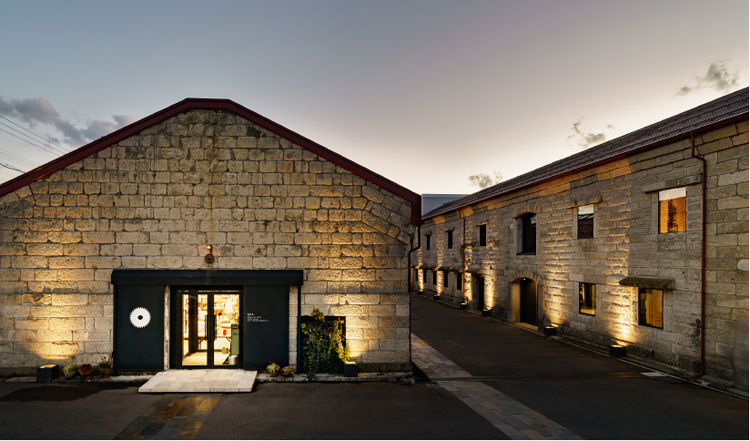